Essential Best Practices for Warehouse Cleaning
In complex warehouse environments, cleanliness – including commercial cleaning – is key for visual appeal, operational efficiency, safety compliance, and productivity. Efficient storage and distribution rely on strict cleaning schedules, including periodic carpet cleaning, to prevent hazardous waste accumulation, mold growth, and debris-related injuries. This article outlines a comprehensive strategy for warehouse managers to develop effective cleaning programs by establishing clear objectives, selecting proper tools, and implementing reliable procedures that incorporate make-ready protocols to balance productivity with compliance while reducing downtime.
Developing Your Warehouse Cleaning Strategy: A Core Best Practice
A robust cleaning strategy begins with clear objectives, defined scope, and custom cleaning schedules tailored to industrial needs, including commercial cleaning solutions. Managers should create plans with measurable targets and performance metrics to cover every cleaning phase—from routine floor sweeping and carpet cleaning to emergency spill management and make-ready procedures.
Defining Scope and Objectives for Optimal Warehouse Cleanliness
Outline the areas and processes the program will cover. Objectives should aim to reduce contamination, improve employee safety by minimizing hazards, and boost operational efficiency through integrated approaches such as commercial cleaning and carpet cleaning. For instance, a goal might be “to reduce slip and fall incidents by 25% over six months” by applying proactive commercial cleaning practices and using non-slip floor coatings. Additionally, incorporating make-ready procedures will ensure that spaces are prepared adequately before operations. Engaging with stakeholders from frontline staff to administration will help set both qualitative and quantitative targets.
Adopting Best Practices for Warehouse Cleaning Frequency and Timing
Cleaning schedules must reflect inventory turnover, peak operating times, and possible contamination sources in settings such as commercial cleaning operations. Best practices include after-shift cleanups, weekly deep cleans—which may involve carpet cleaning—and real-time audits when spills occur to support a make-ready environment. Scheduling cleaning tasks during low-activity periods prevents workflow interruptions, while just-in-time techniques ensure prompt action on emerging hazards.
Assigning Roles and Responsibilities for Cleaning Operations
Clarify responsibilities by defining roles for warehouse staff, including supervisory, housekeeping, and specialist teams (such as biohazard disposal crews who handle commercial cleaning, carpet cleaning, and make-ready operations). Written procedures ensure every employee understands daily tasks and emergency responses, reducing confusion and eliminating overlapping duties.
Selecting Cleaning Methods Aligned With Warehouse Needs
Different warehouses have unique cleaning requirements. In certain facilities, commercial cleaning standards are applied to ensure thorough carpet cleaning and proper make-ready procedures. Dry sweeping may work for low-liquids settings, whereas wet mopping or floor scrubbing is necessary in high-traffic centers. Specialized methods like soft-washing are recommended for delicate surfaces. Choosing the right technique minimizes surface damage and shortens overall cleaning time.
Budgeting for Your Warehouse Cleaning Program
A comprehensive cleaning budget should cover labor, supplies, equipment purchase and maintenance for commercial cleaning, plus specialized services for hazardous waste. Investments in high-quality machines, training, audits, and carpet cleaning initiatives reduce long-term costs by increasing safety and productivity while decreasing breakdowns and downtime. Decision-makers must balance upfront expenses with operational savings, ensuring make-ready processes are in place to maintain cost-effective reliability.
Equipping for Success: Tools and Supplies for Effective Warehouse Cleaning
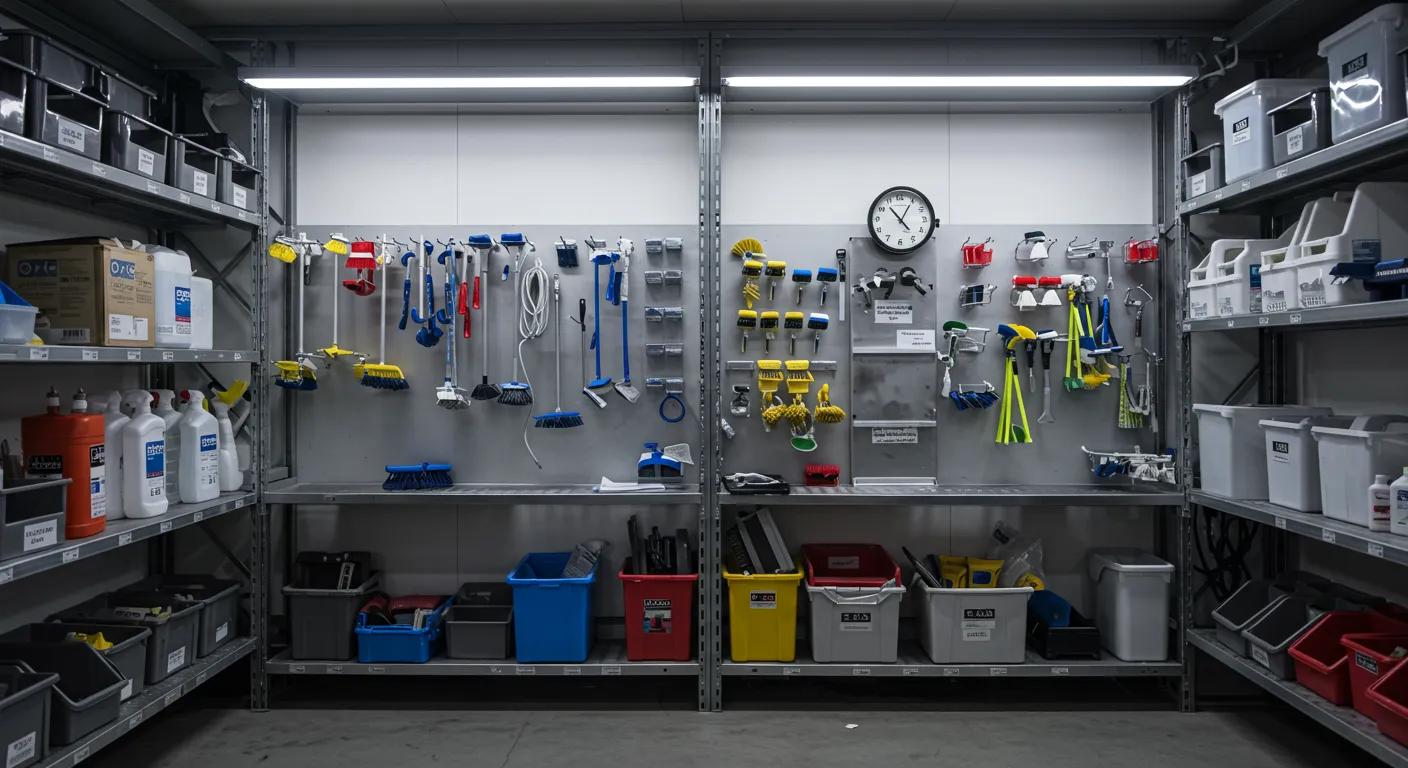
The quality and suitability of cleaning tools and supplies significantly affect overall cleaning outcomes and worker safety in commercial cleaning settings. Using high-quality equipment and supplies enhances process efficacy, whether for tasks such as carpet cleaning or make-ready procedures, and ensures consistent maintenance standards.
Choosing the Right Industrial Cleaning Equipment: A Best Practice
Select equipment based on the warehouse’s specific demands. Floor scrubbers, dust extractors, and high-pressure washers are ideal for various tasks in commercial cleaning projects. For example, heavy-duty, chemical-resistant scrubbers benefit areas with thick grease, while low-impact cleaning devices suit delicate storage zones—especially in carpet cleaning areas. Well-maintained equipment can boost cleaning efficiency, reduce labor costs and downtime during make-ready operations.
Sourcing Safe and Effective Cleaning Agents
Choose cleaning agents that effectively combat dirt, mold, and chemical residues without damaging surfaces, especially in commercial cleaning environments. Environmentally friendly formulas that are non-toxic support both cleaning performance and worker safety. Evaluate agents for pH balance, corrosiveness, and surface compatibility to ensure safe worker exposure while dissolving stubborn residues during carpet cleaning routines and prior to make-ready procedures.
Best Practices for Maintaining and Storing Cleaning Gear
Regularly inspect and clean tools to prolong their lifespan and ensure availability, especially when following commercial cleaning procedures. Implement preventive maintenance schedules for repairs, replacements, and performance evaluations, incorporating make-ready tasks when adjustments are necessary. Maintaining a designated, clearly labeled storage area with controlled conditions prevents material degradation and cross-contamination between cleaning cycles, as seen in routine carpet cleaning operations.
Implementing an Inventory System for Cleaning Consumables
An organized inventory system for items used in commercial cleaning, like disinfectants, paper towels, and air fresheners, ensures timely resupply and prevents shortages. Digital systems offering real-time stock tracking and automated reordering can reduce overhead costs in carpet cleaning and waste, while periodic audits optimize consumption and support make-ready compliance.
Providing Appropriate Personal Protective Equipment
Proper PPE, including gloves, masks, and gowns, is essential for protecting staff from hazardous substances during cleaning and maintenance operations such as commercial cleaning and carpet cleaning. Regular training on proper PPE usage and periodic updates of supplies help reduce occupational risks and comply with OSHA and regulatory standards, further supporting make-ready processes.
Executing Daily and Periodic Cleaning Tasks: Essential Warehouse Practices
Routine cleaning tasks are the backbone of a well-managed warehouse. Incorporating commercial cleaning methods and scheduling routine carpet cleaning for adjacent office spaces, along with periodic make-ready procedures, supports detailed planning that differentiates between daily cleaning and more intensive periodic tasks, ensuring high cleanliness without disrupting operations.
Best Practices for Warehouse Floor Sweeping and Scrubbing
Daily sweeping removes loose dust and debris that create slip hazards and interfere with machinery. For areas with softer surfaces, incorporating carpet cleaning practices ensures even these zones remain free of debris. For deeper cleaning, periodic scrubbing using appropriate agents—an approach common in commercial cleaning protocols—should be scheduled based on traffic and contamination levels. High-performance scrubbers remove grease and stains efficiently, enhancing safety, boosting employee morale, and facilitating make-ready processes. Guidelines should specify methods, sweep frequencies, and techniques to reduce water use and chemical runoff.
Dust and Debris Control on Racking, Shelves, and Products
Regular dusting and wiping of racking systems and shelves prevent dust accumulation that can damage products and complicate inventory management. Incorporating commercial cleaning practices can further enhance the overall hygiene of the space. Using microfiber cloths and low-lint solutions helps remove dust without leaving residues, reducing static electricity buildup and fire risks through careful carpet cleaning measures. An initial broad cleaning followed by make-ready touch-ups in high-use areas is recommended.
Managing Spills and Stains Promptly and Safely
Spills and stains pose immediate slip and chemical exposure risks. Immediate containment, absorption using industrial-grade absorbents in line with commercial cleaning practices, and neutralization with proper cleaning agents are critical. In cases where spills occur on fabric or cushioned surfaces, a focused carpet cleaning approach can ensure deeper treatment of the affected area. Training staff in spill response and keeping accessible spill kits (with PPE, absorbent mats, and neutralizers) minimizes hazards. A clear protocol with immediate supervisor notification, detailed incident documentation, and a subsequent make-ready review is essential.
Waste Management and Recycling: Best Practices for a Tidy Warehouse
Effective waste management goes beyond garbage disposal to include sorting, recycling, and proper material disposal, with a make-ready approach that anticipates further cleanup needs. Clear segregation for paper, plastics, metals, and hazardous waste complies with regulatory standards and supports green cleaning practices. In addition, facilities often rely on commercial cleaning services to address specific requirements such as carpet cleaning in high-traffic areas. Clearly labeled storage zones and coordination with certified recyclers help prevent environmental hazards and maintain a safe warehouse.
Cleaning Loading Docks, Entryways, and High-Traffic Zones
High-traffic areas such as loading docks, entryways, and corridors require special attention due to constant vehicle and pedestrian movement. Using heavy-duty equipment like pressure washers for external surfaces and specialized scrubbers indoors, supplemented by commercial cleaning efforts, minimizes dirt and oil buildup. Incorporating carpet cleaning practices further enhances the maintenance of interior surfaces. Frequent cleaning in these areas, along with a proper make-ready process during loading and unloading operations, reduces accidents and helps protect products.
Prioritizing Safety in All Warehouse Cleaning Operations
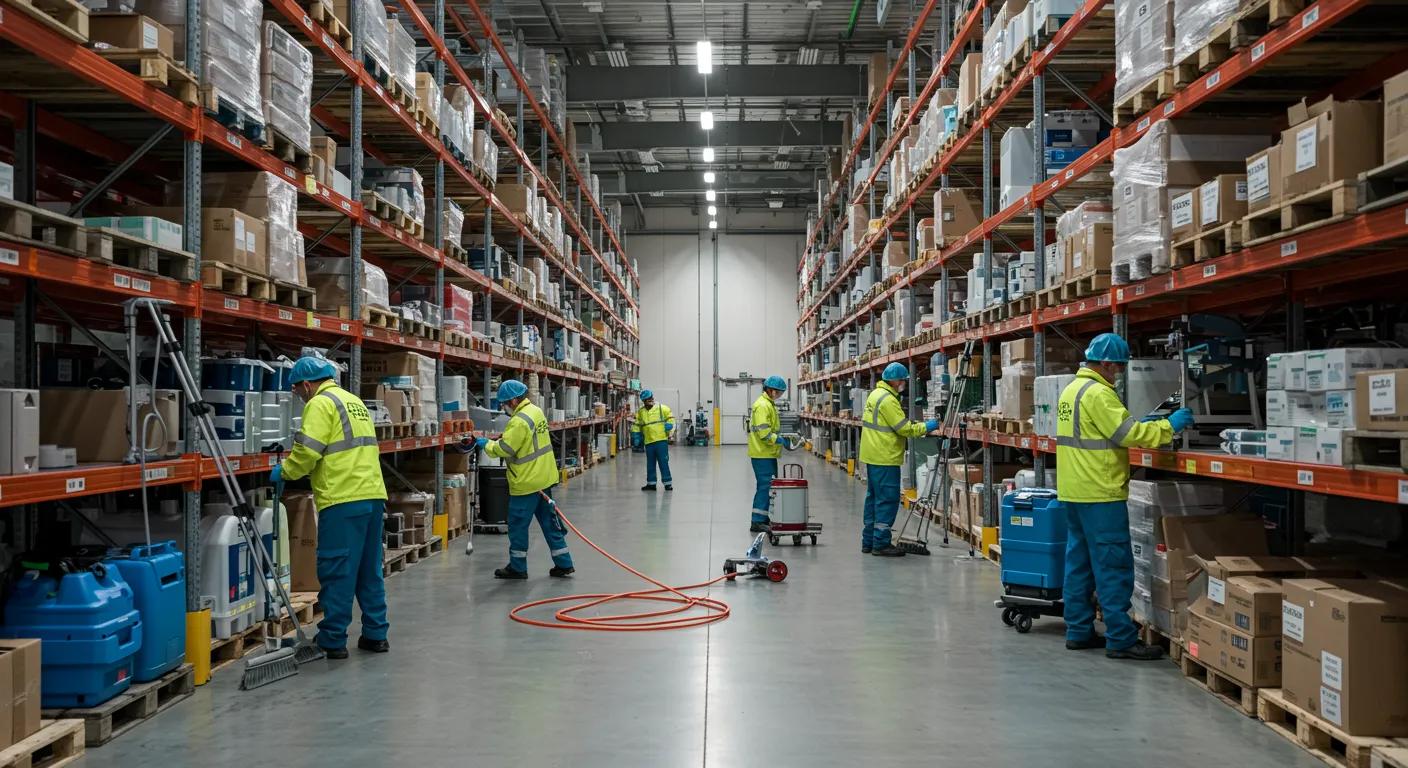
Safety is paramount in cleaning operations. Every task must integrate safety measures to reduce exposure to hazardous chemicals and physical risks.
Chemical Safety Best Practices for Warehouse Cleaning Staff
Staff should be trained to handle, mix, and store chemical cleaning agents used in commercial cleaning safely by following Material Safety Data Sheets (MSDS) and OSHA standards. Protective gear, clear labeling, and secure storage are essential not only for general cleaning tasks but also for carpet cleaning practices. In the event of spills, a documented response plan including make-ready procedures, neutralization procedures, and incident reporting must be in place to ensure a safe work environment.
Preventing Slips, Trips, and Falls During Cleaning
Employee safety during cleaning, particularly in commercial cleaning settings, is enhanced by using non-slip mats and placing warning signs in wet or high-risk areas. Regular training on proper cleaning techniques—including expertise in carpet cleaning—is essential for maintaining security and reducing trip hazards. Monitoring and analyzing injury incidents, along with timely make-ready procedures, help adjust schedules and methods to further prevent accidents.
Ensuring Proper Ventilation and Air Quality
Good ventilation and proper HVAC systems are crucial, especially when using chemical agents in commercial cleaning processes. Routine air quality tests and the strategic placement of industrial fans or scrubbers help maintain a healthy environment by preventing the buildup of dust, residues from carpet cleaning, and chemical vapors, thereby safeguarding worker health and stored goods. Additionally, make-ready procedures ensure that spaces are properly prepared for ongoing operations.
Safe Operation and Storage of Cleaning Machinery
Only trained personnel should operate heavy machinery such as floor scrubbers, vacuum systems, and pressure washers, particularly in commercial cleaning environments. Regular maintenance, clear user manuals, and proper storage reduce equipment-related accidents during tasks like carpet cleaning. Enforcing safety protocols, including emergency shut-off systems and regular audits, helps keep machinery in compliance, minimizes downtime, and supports effective make-ready procedures.
Emergency Preparedness for Cleaning-Related Incidents
A clear emergency preparedness plan is essential for handling incidents like chemical spills or equipment malfunctions. This plan should document evacuation routes, emergency contacts, and staff roles. Additionally, incorporating commercial cleaning and carpet cleaning procedures into the emergency protocol can greatly mitigate the aftermath of spills. Regular drills, updated first aid kits, and accessible emergency equipment—such as fire extinguishers, make-ready protocols, and spill containment materials—further ensure a quick and effective response to emergencies.
Addressing Specific Zones: Tailored Best Practices for Warehouse Cleaning
Different warehouse zones require specialized cleaning approaches to maintain their specific standards.
Maintaining Cleanliness in Storage and Picking Areas
Storage and picking areas, critical to warehouse operations, require routine dusting, mopping, carpet cleaning, and spot-cleaning as part of a make-ready process to prevent contamination. Using air filtration and dust extraction systems, along with commercial cleaning protocols and detailed audit checklists for high-contact surfaces, improve organization and reduce errors in inventory handling.
Best Practices for Office and Amenity Cleaning Within the Warehouse
Office spaces, break rooms, and restrooms require different cleaning protocols, including commercial cleaning practices, to maintain employee morale and health. Frequent disinfection, regular vacuuming, and carpet cleaning of high-contact surfaces are essential. Additionally, maintaining HVAC filters and implementing make-ready procedures for toiletries further contribute to a hygienic workspace.
Specialized Cleaning for Cold Storage or Regulated Environments
Cold storage and regulated environments, such as areas handling perishables or pharmaceuticals, need protocols that protect temperature-sensitive goods, including make-ready procedures to ensure optimal sanitization. Specialized agents with expertise in commercial cleaning and carpet cleaning techniques are used to avoid temperature fluctuations while ensuring microbial contaminants are removed. Adhering to strict health guidelines and regulatory standards, along with regular third-party audits, maintains high standards in these areas.
Exterior Maintenance: Keeping Surrounding Areas Clean
Exterior zones—including loading docks, entryways, parking lots, and landscaped areas—affect overall facility perception and safety. Scheduled pressure washing, strategically placed waste bins, and regular inspections as part of commercial cleaning not only help keep the surroundings free from oil, debris, and stains but also ensure the facility is make-ready, with interior tasks like carpet cleaning further enhancing the overall safety and appeal for pedestrians.
Pest Control Integration With Cleaning Best Practices
Regular inspections, sealing entry points using effective make-ready procedures, and the strategic use of traps and repellents are essential to prevent pest infestations that could lead to product contamination, especially in areas that benefit from routine carpet cleaning. Coordinating with professional pest management services—including commercial cleaning initiatives—and educating staff on early signs of pest activity ensure proactive intervention and long-term prevention.
Sustaining High Standards: Continuous Improvement in Warehouse Cleaning
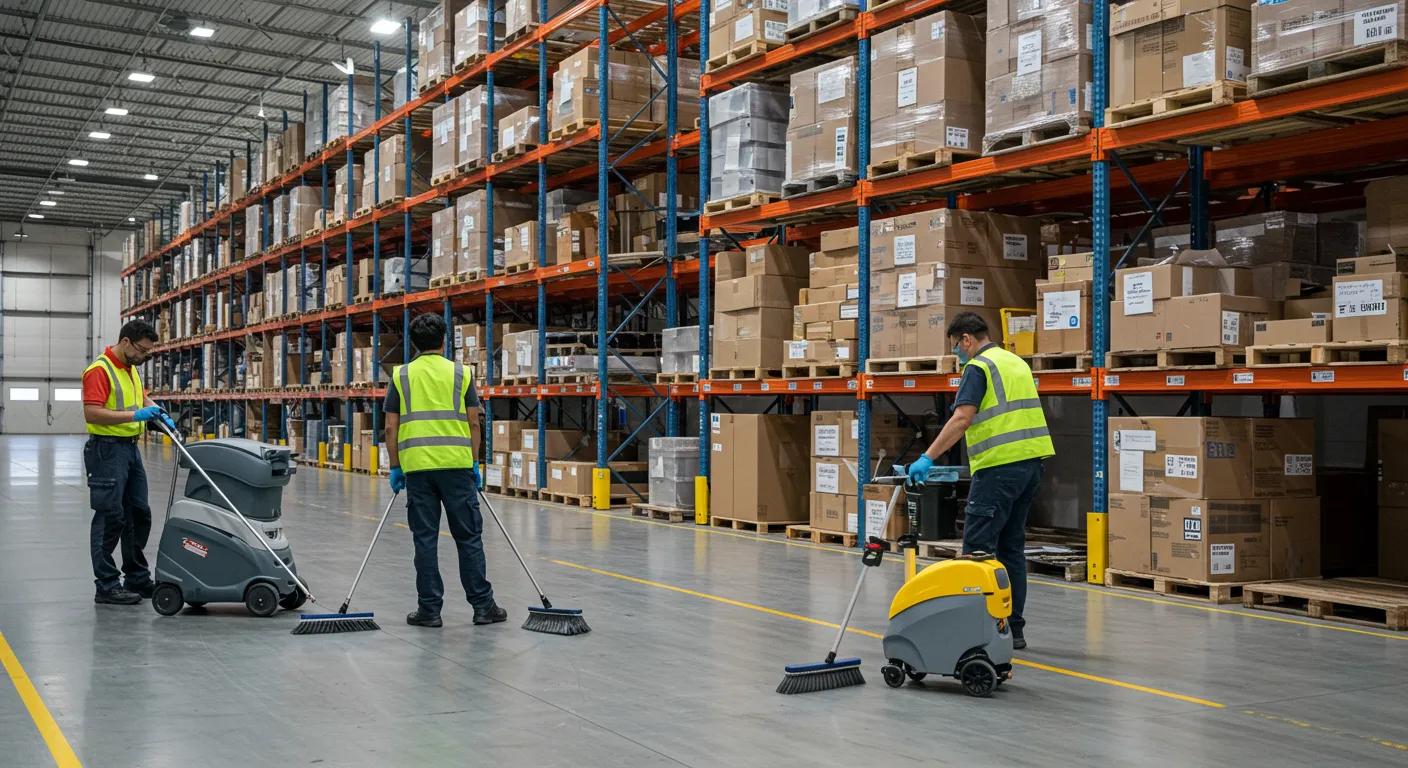
Ongoing audits, regular training, and process optimizations are crucial to adapt cleaning protocols to evolving operational demands and technological advancements.
Conducting Regular Cleaning Audits and Inspections
Regular audits by quality control teams help identify weaknesses in commercial cleaning procedures such as equipment wear or inconsistent cleaning frequency. Establishing cleanliness scores, implementing carpet cleaning protocols, and documenting audits in a centralized system ensures ongoing regulatory compliance and highlights opportunities for cost savings, including more efficient make-ready processes.
Training and Empowering Staff in Cleaning Best Practices
Continuous education on new techniques, safety protocols, and operational procedures, particularly in commercial cleaning, is key to maintaining high standards. Involving staff in decision-making and rewarding exceptional performance in carpet cleaning and make-ready tasks foster a culture of accountability and quality.
Gathering Feedback for Refining Cleaning Procedures
Implement structured feedback systems for commercial cleaning through suggestion boxes, meetings, and surveys. Frontline employees, particularly those involved in carpet cleaning, can offer practical insights that help refine cleaning practices, ensuring that processes remain responsive to real-world challenges like make-ready protocols.
Adopting New Technologies for Better Warehouse Cleaning Outcomes
Embrace automation—such as robotic scrubbers and sensor-equipped devices used in commercial cleaning—to reduce human error and enhance cleaning efficiency, especially in carpet cleaning operations. Data-driven systems for monitoring environmental conditions and smart inventory management facilitate informed decisions that lower operating costs and improve hygiene, ensuring a smooth make-ready process for spaces in need of rapid turnaround.
Documenting and Standardizing Your Best Practices for Warehouse Cleaning
Create detailed manuals, checklists specifically for commercial cleaning, and standard operating procedures to ensure uniformity across shifts and locations. Regularly update these documents to reflect current industry standards and regulatory requirements, including guidelines for carpet cleaning. A centralized repository assists in training, audits, and make-ready procedures while promoting consistency and transparency.
Table: Comparison of Warehouse Cleaning Tools and Supplies
Before reviewing each element, consider the table below which compares common cleaning tools and highlights their benefits:
List: Essential Warehouse Cleaning Supplies and Their Uses
Below is a concise list of key supplies every warehouse should maintain:
- Disinfectant Solutions – High-Performance Sanitation: Eliminate bacteria, mold, and chemical residues on high-touch surfaces to prevent disease outbreaks.
- Industrial-Grade Absorbents – Spill Management: Quickly contain and neutralize liquid spills, reducing slip risks and chemical exposure.
- Microfiber Cloths and Mops – Dust and Debris Control: Capture dust and dirt without scratching surfaces, ensuring a streak-free finish.
- Non-Slip Mats and Warning Signage – Safety Enhancement: Warn staff of wet areas and reduce slip, trip, and fall accidents in high-water zones.
- PPE Kits – Employee Protection: Provide gloves, masks, and eyewear to safeguard against chemical exposure and comply with OSHA standards.
Frequently Asked Questions
Q: How often should warehouses conduct deep cleaning? A: Deep cleaning should occur at least monthly, with daily maintenance. Some facilities may opt for bi-weekly or weekly deep cleaning based on inventory turnover, clutter, and incident reports. In addition, regular commercial cleaning can help maintain high standards, especially when paired with specifics such as carpet cleaning to ensure thorough upkeep and a smooth make-ready process.
Q: What cleaning equipment is most effective in large warehouse environments for commercial cleaning? A: High-performance floor scrubbers, industrial dust extractors, and pressure washers are most effective, particularly in areas requiring carpet cleaning. Their robust design reduces cleaning time and labor costs while enhancing safety and streamlining make-ready processes.
Q: How can a warehouse minimize the risk of slip and fall accidents during cleaning? A: Use non-slip mats, manage spills immediately, ensure proper ventilation, and schedule cleaning during low-traffic periods while training staff on safe practices. For instance, incorporating make-ready procedures during commercial cleaning can help prevent hazards, and periodic carpet cleaning further reduces risks on frequently trafficked areas.
Q: What steps should be taken to ensure the proper disposal of hazardous cleaning waste? A: In commercial cleaning operations, it is essential to separate and store hazardous waste in designated containers. When engaging in tasks such as carpet cleaning, always perform the necessary make-ready procedures to ensure safe handling before disposal through certified companies. Regular audits and detailed documentation help ensure compliance with environmental standards.
Q: How do warehouses maintain compliance with osha during cleaning operations? A: Compliance is achieved through proper ppe training, safe chemical handling, machine operation protocols, regular inspections, and thorough record-keeping of cleaning procedures. Additionally, many facilities incorporate make-ready checks as part of their routine, ensuring that both commercial cleaning and carpet cleaning standards are met.
Q: Can automation improve warehouse cleaning processes, including commercial cleaning and make-ready tasks? A: Yes. Robotic scrubbers and sensor-based systems improve efficiency by reducing human error and enabling data-driven scheduling adjustments. These advances also streamline operations in areas such as carpet cleaning, ensuring a more consistent overall maintenance process.
Q: What are the long-term benefits of a well-maintained warehouse cleaning program? A: Such programs boost operational efficiency, enhance employee safety, reduce downtime, improve facility appearance (notably through carpet cleaning), and lead to cost savings through better regulatory compliance. In addition, integrating commercial cleaning strategies and a dependable make-ready process can further streamline operations and elevate overall facility standards.
Final Thoughts
This article has detailed essential best practices for warehouse cleaning—from strategy development to daily operations—while maintaining high safety standards, continuous improvement, and a make-ready approach. By investing in the proper equipment, supplies, and training, including regular carpet cleaning, organizations can boost operational efficiency and productivity. Embracing advanced cleaning technologies and regular audits ensures compliance with safety regulations and results in a secure, efficient working environment. These guidelines provide a pathway to operational excellence in commercial cleaning.
Sign up for our affiliate program and watch your earnings grow! https://shorturl.fm/hVUt9
Your influence, your income—join our affiliate network today! https://shorturl.fm/JJlL1
Maximize your income with our high-converting offers—join as an affiliate! https://shorturl.fm/obfWd
Unlock exclusive rewards with every referral—apply to our affiliate program now! https://shorturl.fm/fiThv
Start earning instantly—become our affiliate and earn on every sale! https://shorturl.fm/9irgK
Drive sales and watch your affiliate earnings soar! https://shorturl.fm/upZiD
Get paid for every referral—enroll in our affiliate program! https://shorturl.fm/zwySS
Join our affiliate program and start earning today—sign up now! https://shorturl.fm/jI62N
Boost your income effortlessly—join our affiliate network now! https://shorturl.fm/DXJq6
Join our affiliate program today and start earning up to 30% commission—sign up now! https://shorturl.fm/9g6Wc
Unlock exclusive affiliate perks—register now! https://shorturl.fm/Yd9eN
Monetize your audience—become an affiliate partner now! https://shorturl.fm/b2etG
Start earning instantly—become our affiliate and earn on every sale! https://shorturl.fm/zPCBx
Join our affiliate community and earn more—register now! https://shorturl.fm/1T5FM
Start profiting from your network—sign up today! https://shorturl.fm/N7XQ7
Unlock top-tier commissions—become our affiliate partner now! https://shorturl.fm/fwPWT
Tap into unlimited earnings—sign up for our affiliate program! https://shorturl.fm/3M3VU
Share your unique link and earn up to 40% commission! https://shorturl.fm/iOxfy
Get started instantly—earn on every referral you make! https://shorturl.fm/p3yZp
Share your link, earn rewards—sign up for our affiliate program! https://shorturl.fm/rTVOB
Become our partner now and start turning referrals into revenue! https://shorturl.fm/DtsWs
Get started instantly—earn on every referral you make! https://shorturl.fm/5Wgxa
Monetize your influence—become an affiliate today! https://shorturl.fm/9u2TK
Start sharing, start earning—become our affiliate today! https://shorturl.fm/46X7V
Partner with us and enjoy recurring commission payouts! https://shorturl.fm/jTV31
Unlock exclusive rewards with every referral—apply to our affiliate program now! https://shorturl.fm/60tx2
Boost your income—enroll in our affiliate program today! https://shorturl.fm/QCpNP